摘 要:本文介绍了涡流检测技术原理及主要特点,提出在役换热器换热列管的检测实施要点,并就该技术在合成氨装置中的实际检测应用作简要介绍。
关键词:换热列管 涡流检测
0 前 言
在合成氨生产装置中,广泛使用着各种形式的列管式热交换器,其中有不少换热器在高温、高压及腐蚀介质中运行。由于介质腐蚀、冲刷、疲劳应力等作用,会使列管管壁产生各种腐蚀缺陷、损伤和壁厚减薄,这将严重威胁设备的安全运行。
而由于设备结构的特殊性或系统装置条件的不具备,很多换热器不能进行常规的壳侧水压或气压试验,无法准确查找出换热管的泄漏部位,更不能对换热列管可能存在的隐患作出有效的预报性诊断。
因此,采用涡流检测技术对这些在役换热器的换热列管进行定期检测,掌握列管缺陷的存在及发展情况,掌握列管最小壁厚值的变化情况,从而对换热列管使用状况作出有效的预防性诊断及处理,是保证装置生产设备长周期安全运行的可靠技术手段。
1 涡流检测技术原理
涡流检测技术的理论基础是电磁感应。
载有交变电流的检测线圈靠近导电试件时,由于激励线圈磁场的作用,将会在试件中感应出涡流(见图1);而涡流的大小、相位及流动形式受到试件导电性能的影响,同时产生的涡流也会形成一个磁场,这个磁场反过来又会使检测线圈的阻抗发生变化。
通过测定检测线圈阻抗的变化,就可以判断出被测试件的性能及有无缺陷。
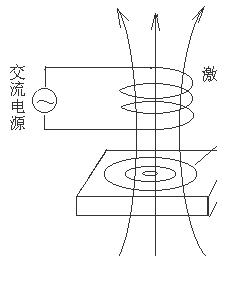
图1 涡流检测的原理
对在役换热列管的涡流检测,采用内穿过式线圈作为“检测探头”,通常由两个或两个以上的测量线圈组成。
对列管进行涡流检测时,线圈中加载的交变电流将在列管壁上形成涡流场(见图2);而列管的几何缺陷、电磁异常和壁厚变化等因素都将对该涡流场形成影响。
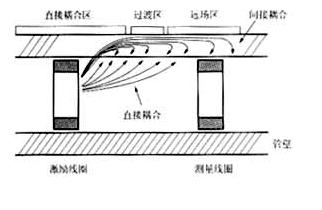
图2 列管涡流场形成示意图
当列管无影响涡流场的因素存在时,涡流场无变化,两个测量线圈反向连接感应电压为平衡状态,没有输出;当列管存在影响涡流场的因素时,涡流场的变化又使测量线圈的阻抗和感生电压发生改变。
测出阻抗变化量,经过仪器处理可判列管的缺陷情况——涡流探伤;
测出感生电压变化量,就可得出列管壁厚的变化状况——涡流测厚。
2 涡流检测技术类型
涡流检测技术手段分为两大类型:常规涡流检测和远场涡流检测。
2.1 常规涡流检测
适用于纯奥氏体不锈钢、纯钛及其合金、纯镍及其合金、铜、铝等非铁磁性材料。
常规涡流场形成于“近场区”,其涡流信号具有趋肤效应及在深度方向的相位滞后效应。
利用相位滞后效应,在检测参数合适的前提下,通过建立对比试样管上不同深度人工模拟缺陷的阻抗图及缺陷深度—相位图(见图3、图4),可在涡流探伤时有效区分列管壁缺陷的性质及类型。
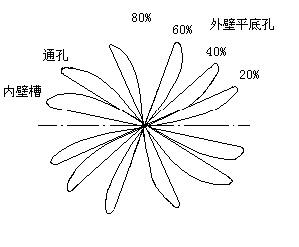
图3 常规涡流缺陷阻抗图
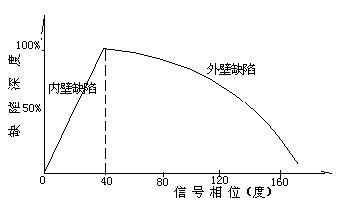
图4 常规涡流缺陷深度—相位曲线图
2.2 远场涡流检测
远场涡流技术基于一种特殊物理现象——远场涡流效应,是一种能穿透金属管壁的低频涡流检测技术。
特别适用于奥氏体-铁素体双相不锈钢、铁素体不锈钢、Cr-Mo钢、碳钢等铁磁性材料。
检测换热列管时,内置式探头置于被检测管内,探头上有一个激励线圈,还有一个(或二个)测量线圈;激励线圈和测量线圈的距离为列管内径的2-3倍。
激励线圈通以低频交流电,发出的磁力线(能量)穿过管壁向外扩散,在远场区又再次穿过有表面缺陷的管壁向内扩散,被测量线圈接收(见图5)。
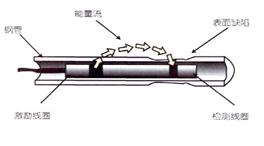
图5 远场涡流场能量传递示意
若管子壁厚为h,则磁场两次穿过管壁造成的振幅衰减和相位滞后由下式决定
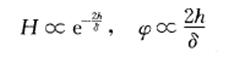
H—磁场强度振幅衰减值
δ—集肤深度
φ—测量线圈感应电压和激励电流间的相位滞后值
由上式可见:若管壁存在裂纹、凹坑及腐蚀等缺陷,则相应部位管壁厚度减小,导致检测信号相位滞后值减小,振幅衰减值增大。
据此,可以根据检测信号相位及幅值的变化,判断被检测换热管缺陷状况。
2.3 远场涡流和常规涡流技术的比较
1)测量磁场区域:
常规涡流线圈置于直接耦合区,测量的是传播到管壁又直接返回的磁场。
远场涡流为避免直接磁耦合,测量线圈必须置于远离激励线圈的间接耦合区,测量穿过管壁后在管外沿管轴传播一段距离返回管内的磁场。
因此,远场涡流检测独具有透壁性,能检测整个管壁上的缺陷而不受集肤效应的限制,克服了电导率和磁导率的影响,对内外壁的缺陷具有相同的灵敏度,且相位信号不受提离效应的影响。同时,对填充系数要求低,对探头在管内行走产生的偏心影响很小。
2)检测频率:
远场涡流检测采用较低的频率(典型为50~500Hz),磁场穿过铁磁性材料管壁,不受管壁厚度影响。
常规涡流检测频率较高(千赫范围),受趋肤效应制约,磁场被限制在管壁有限厚度内,检测厚壁列管外部缺陷较为困难。
3 涡流检测技术特点
3.1 涡流技术在换热列管检测应用中的优越性
1)非接触式无损检测,是检测在役换热列管的最行之有效手段。
2)检测速度快,灵敏度高。
3)检测信号为电信号,可进行数字化处理,便于存储、再现及进行数据比较和处理。
4)涡流探伤时,通过对检测信号的相位-幅值分析,可就缺陷信号所表征的缺陷性质、类型、大小进行有效判定。
5)涡流测厚时,可实时显示换热列管全长的壁厚分布状况,并自动记录最薄截面的壁厚数据为检测值,测量误差在±0.05mm内。
3.2 涡流技术在换热列管检测应用中的局限性
1)需要制作专门的对比样管进行检测基准的校准。
2)受涡流所特有的末端效应的影响,离换热管口一定范围内检测信号将严重畸变,无法正确识别出缺陷,一般称此部位为涡流检测的“盲区”。
3)对于U型管,由于探头自身的长度与刚性原因,无法穿入U型弯管的中心较小弯曲半径段,故此区域管段无法进行涡流检测。
4)涡流检测信号只表征换热列管母材自身的变化状况,无法反映出管子-管板角焊缝的状态,不能用于查找角焊缝的相关缺陷。
5)采用内穿过式线圈时,对缺陷所处圆周上的具体位置无法判定;采用旋转探头式检测虽可定位,但检测速度慢。
4 涡流检测系统组成
涡流检测系统由检测主机、数据分析系统、检测传感器(探头)及对比样管组成。
4.1 检测主机(以ET556H为例)
用阻抗平面显示,能实时得到缺陷信号的李萨育图形,全面反映检测信号的幅值、相位。
利用相位分析技术,可将干扰与缺陷信号分开,提高信噪比。
激励频率范围宽广可调(50Hz~1MHz),相位3600可调范围。
采用自动平衡技术。
具备多频检测功能,可以有效抑制干扰
4.2 数据分析系统
利用计算机进行检测信号处理,具备混频、报警设定、相位-幅值分析、数值存储记录等适时数据自动分析处理功能。
采用专门开发设计的检测软件,可自动完成换热列管壁厚的求平均值、分类、统计等工作,并生成各类直观的数据分布图;通过对分布图的分析,可以了解设备管子的壁厚分布情况和腐蚀情况,从而分析引起腐蚀的设备和工艺因素。
4.3 检测传感器
涡流探伤时,采用自比较式差动线圈;涡流测厚时,采用绝对式线圈。
一般情况下采用普通内穿过式,特殊情况下采用内壁旋转探头式。
4.4 对比样管
用来校验仪器检测参数,保证检测模型的精确性。
通常采用与被检测换热器列管相同材料及规格的管段进行加工,特殊情况下可代用,但必须由具有丰富检测经验的技术人员依据理论计算值进行检测偏差调整。
对比样管按相关标准规定结构形式,根据具体检测要求进行设计;采用数控、线切割等高精尖加工手段,控制加工误差满足相关标准的规定。
检测使用的对比样管,必须能准确模拟被检换热列管的各种可能缺陷、壁厚减薄范围。
5 在役换热器列管涡流检测的目的及内容
5.1 检测目的
对在役换热器的换热列管进行涡流检测,实现一下检测目的:
1)可估价换热列管的全面工作状态,并通过常规检查来评价某种状态可能进一步恶化的情况。
2)定量评价由于水或溶液的化学成分和设备运行情况的变化而使换热列管产生变化的状态、变化的速率以及设备的腐蚀速率,推算换热器列管的剩余寿命。
3)研究整个换热器换热列管的缺陷和腐蚀的分布状态,以帮助分析并确定引起换热器的状态恶化及泄漏的原因。
4)为确定是否需要修理和进一步在适当的时候换管提供有用的资料。
5.2 检测内容
1)涡流探伤:检测换热列管是否存在裂纹、蚀坑、机械损伤等缺陷,评定缺陷的类型、大小及性质。
2)涡流测厚:检测换热列管全长的壁厚变化状态,准确查找出最薄截面位置并确定残余壁厚值,判断列管壁的腐蚀状态、腐蚀程度。
3)综合以上两项检测内容,可准确判断本次检测时是否存在需要报废处置的部件或设备,并预判在下一运行周期内换热列管可能的腐蚀发展或是否可能出现泄漏,为换热器安全运行提供可靠依据。
6 在役换热器列管涡流检测的实施要点
6.1 检测方案的制订
不同工艺介质及运行特点、不同换热列管材质及壁厚的换热器,其主要腐蚀特征及损坏形式均不相同。
因此,必须根据设备结构特点及工艺运行状况、换热列管材质及壁厚、换热列管表面状态等因素,结合相应的检验标准或规范,综合制订检测方案。
在检测方案中,需规定:检测主要目的、检测系统、检测参数、检测程序、检测评判标准及检测报告形式。
6.2 对比样管的标定
对比样管的标定信号为现场检测信号分析处理的基本依据。
检测前,必须先通过检测频率、相位、增益等参数的设定,将对样管进行标定,获得最佳检测信号,以建立有效的检测数据模型。
6.3干扰的抑制
由于换热列管周围有管板和支撑板环绕,将会对检测造成一定干扰。如果列管上恰在此部位存在缺陷,则干扰信号将会与缺陷信号叠加形成复合信号而难于判别,有时甚至会淹没缺陷信号,因此必须抑制干扰。
常用的有效方法是采用混频技术。
6.4 涡流探伤缺陷的评定
对检测发现的缺陷信号进行评定是涡流探伤最关键的技术,尤其对多信号叠加形成的复合信号更难于分辨。
这就要求技术人员有丰富的检测经验和对所测设备的充分了解,
在实际检测中,常规涡流由于存在集肤效应及深度方向的相位滞后,因此用对比试样对检测系统进行合适的调试后,依据缺陷信号的相位及幅度大小,可明确地区分缺陷的位置及深度,即缺陷是否穿透,是位于管子的内壁还是外壁及其大小等。
远场涡流检测技术由于不存在常规涡流检测的集肤效应及深度方向的明显相位滞后,因此通过相位变化来区别缺陷位于换热管的内壁或外壁较为困难,也不能准确确定缺陷深度;只能通过实际检测信号与模拟缺陷信号在相位和幅值上的差异,分析缺陷造成的金属损失体积量,从而 “当量”评判缺陷程度。
由于远场涡流场分布的特点,即使换热管上体积损伤量相同的缺陷,由于在分布方向和表现类型上的不同,也会影响缺陷的检出和判定。
若换热管上缺陷相当接近其铁磁性材料制作的支撑板,则受场效应的影响,支撑板信号将严重干扰实际缺陷信号,造成实际缺陷的有效检出及正确识别相当困难。与此类似,管束边缘的换热管,其缺陷信号也容易受到设备筒体上铁磁性结构件的信号干扰。
远场涡流检测时,对换热管轴向裂纹的漏检可能性比较大。这是由于激励线圈产生的电磁场沿换热管轴向平行传播,对于换热管轴向裂纹,一方面其总的金属体积损失量较小,另一方面缺陷切割场流较小,在探头上激励的相对电压变化较低,测量线圈接收信号不大明显。
6.5 涡流测厚数据分析
涡流测厚时,事先在软件内输入换热器管板图文件,按一定次序逐根检测,数据分析系统直接读取涡流信号并显示为测厚曲线,同时转换成壁厚数值并实时对应显示、存储。
涡流测厚软件所记录的壁厚数值,为此列管的最薄截面的壁厚平均值;同时,在检测过程中依据测厚曲线的变化,可分析列管全长的壁厚变化趋势。
受现场环境因素的影响,涡流测厚曲线有时会发生漂移,从而导致检测误差的存在。这就要求检测人员能迅速判断出此误差并及时采取措施纠正测厚曲线的漂移,以保证检测模型的稳定性
7涡流检测技术在合成氨装置在役换热列管中的工程应用实例
7.1检测工程业绩简介
作为国内最早在石化行业进行在役换热列管涡流检测工程应用的检测单位之一,重庆奥林特机电技术有限公司运用常规和远场涡流检测技术,在全国范围的不同领域进行了大量的涡流检测工程实践;尤其是在具有较大技术难度的铁磁性材料换热列管远场涡流检测方面,积累了丰富的经验。
公司在换热列管涡流检测方面所服务的领域包括石油、石油化工、化肥、甲醇及其他各不同类型化工装置,服务厂家包括国外独资、中外合资、大型国企等中外知名企业,并与中石油、中石化、巴斯夫、BP等世界性大公司形成了长期合作伙伴关系。
检测换热器近200台次/年,检测的换热列管材料包括纯奥氏体不锈钢、铜合金、纯钛及钛合金、纯镍及镍基合金、哈氏合金、锆-不锈钢复合金属等非铁磁性材料和碳钢、铬钼钢、铁素体-奥氏体双相不锈钢等铁磁性材料,涉及的换热管形式有直管、U型管、翅片管,换热器型式有固定管板式、浮头式、U型管式。
在合成氨生产装置中,我们已经成功地对以下在役换热器列管进行了多次涡流检测:
第一废热锅炉、第二废热锅炉、合成再沸器、冷却水处理器、碳酸钾溶液再沸器、碳酸钾溶液辅助再沸器、分子筛再生加热器、再生塔再沸器、原料气及循环气一段氨冷器、原料气及循环气二段氨冷器、原料气及循环气三段氨冷器、氨合成塔进气原料气换热器、氨合成塔进气出气换热器、氨合成塔出口锅炉给水换热器、惰性气洗涤器、冷水加热器、合成气水冷器、氨压机出口氨冷器、氨合成塔底部换热器、水煤气换热器、低压废热锅炉等。
7.2检测应用实例
1)常规涡流探伤:
以某厂合成再沸器(105CB)检测为实例。
该换热器为浮头式,换热列管材料为SA249 TP316SS型不锈钢,规格¢19.05×1.65×4000,共2400根,其中检测前已堵管22根。
换热器管程介质为MDE溶液,壳程介质为变换气(氮气、氢气)。
检测时,采用ET-556型数字多频涡流仪,对比样管为TP316L型不锈钢,规格¢19.05×2.11 孔型,检测传感器为高频差动内穿过式,人工拉动探头。
经参数调节后,获得对比试样管上人工模拟缺陷检测信号阻抗图类图3,并据此建立缺陷信号深度-相位曲线图类图4。
实际检测结果为:12根列管存在可计性缺陷信号,其中A级缺陷8根,D级缺陷4根。
其中:管号为55-26的列管,于离下管口约1.5米附近,获得缺陷信号阻抗图如图6。
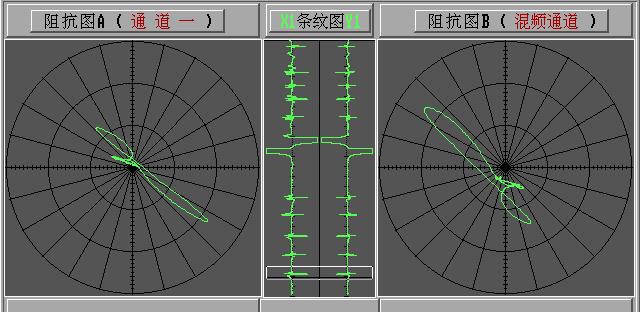
图6 合成再沸器列管55-26涡流探伤信号
检测判定该缺陷级别为D级,具备穿透性;抽出列管后证实检测判定无误(见图7)。
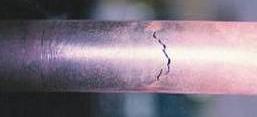
图7 合成再沸器列管55-26穿透性裂纹
2)远场涡流探伤:
以某厂合成气废热锅炉检测为实例。
该换热器为固定管板式,列管材料为16Mo3,规格¢30×2.5×5400,共876根。
管程介质为工艺合成气,壳程介质为蒸汽。
检测时,采用ET-556型数字多频远场涡流仪,对比样管为16Mo3 ¢30×2.5 模拟缺陷分布为通孔、平底孔、环槽、平槽,检测传感器为内穿过式,人工拉动探头。
经参数调节后,获得对比试样管上人工模拟缺陷检测信号阻抗图如图8~11。
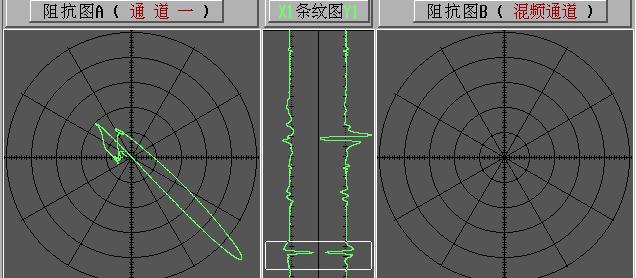
图8 对比试样上通孔信号
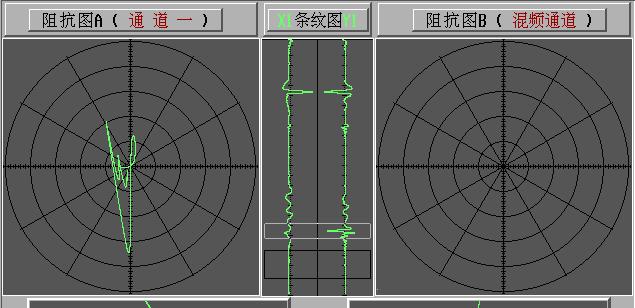
图9 对比试样上40%单边锉槽信号
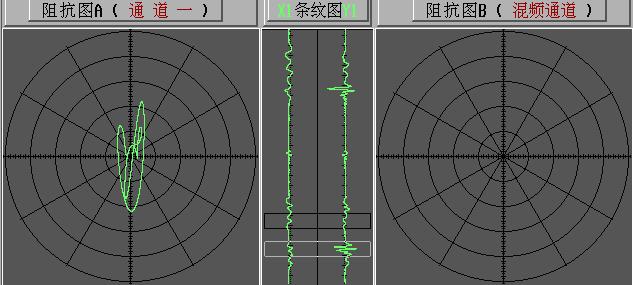
图10 对比试样上20%平底孔信号
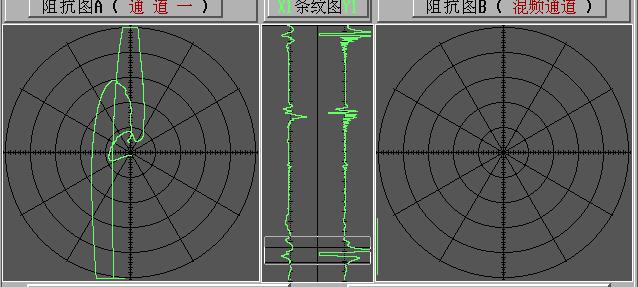
图11 对比试样上20%环槽信号
实际检测结果为:25根列管存在可计性缺陷信号。
其中:管号为25-12的列管,于离下管口约1.2米处,获得缺陷信号阻抗图如图12。
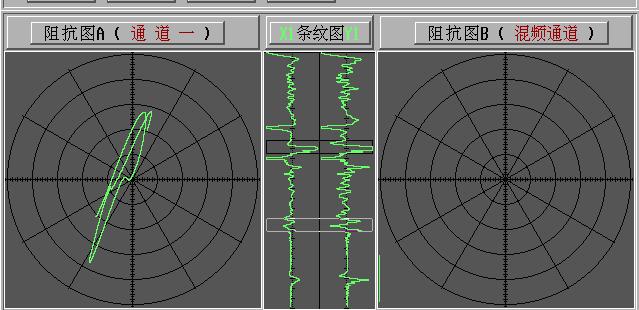
图12 合成气废热锅炉列管25-12涡流探伤信号
可以看出:缺陷信号幅值接近于对比样管上20%平底孔人工缺陷,但相位角大于20%环槽人工缺陷。
检测判定该缺陷深度不到壁厚的20%,系外壁磨蚀造成的局部浅表缺陷。
3)涡流测厚:
仍以某厂合成气废热锅炉检测为实例。
检测时,采用ET-556型数字多频远场涡流仪,对比样管为16Mo3 ¢30×2.5 厚度为2.5/2.0/1.5,检测传感器为内穿过式,人工拉动探头。
检测结果统计为:最大壁厚2.60 mm,最小壁厚2.05 mm,平均壁厚2.44 mm。
检测获得某列管测厚曲线如图13。
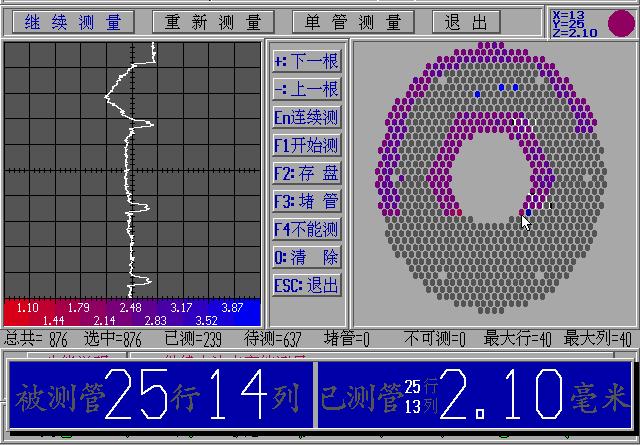
13 换热列管涡流测厚曲线
仪器自动记录最薄截面平均值2.10mm为该列管壁厚测量值。
由图13可以分析出:该列管存在明显减薄区,减薄区位置在下管口往上600~1000mm范围;与同一列管上其他壁厚均匀的管段部分相比,减薄值在0.3mm~0.35mm左右。
全部被检列管的壁厚数据分布图见图14。
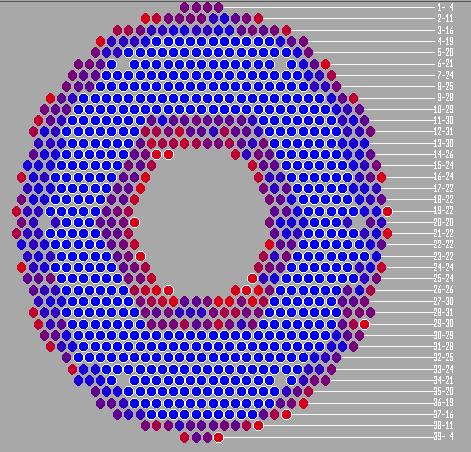
图14 换热列管涡流测厚数据分布管板图
结束语
1)作为一种先进的无损检测技术手段,涡流检测技术对在役换热器换热列管的检测具有不可替代的应用前景。
2)多年的检测经验表明:有计划地对重要设备进行定期检测,能够预先发现潜在的缺陷,掌握设备的实际腐蚀状况并预测其残余寿命。