摘 要:本文介绍了国内首例ACES装置高压甲铵冷凝器双相不锈钢换热列管的管子-管板角焊缝大规模修复案例,结合具体的修复实施过程,指出修复重点环节的技术要求。
关键词:高压甲铵冷凝器 管子-管板角焊缝 双相不锈钢焊接
前言
陕西渭河重化工有限责任公司尿素装置,采用日本东洋工程公司(Toyo Engineering Co.)ACES工艺流程,于1997年建成投入运行至今。
高压设备中,甲铵冷凝器为固定管板式换热器,两台立式并联(位号分别为EA101/102),内部耐蚀材料为DP-12型双相不锈钢,制造焊接材料为SUS329型双相不锈钢。
经过长期使用后,其管子-管板角焊缝出现大面积腐蚀缺陷,局部已经存在泄漏征兆,严重威胁到设备的安全运行。并且,国外同样设备已经出现了因管子-管板角焊缝腐蚀造成的严重泄漏事故。
2009年3月,在渭化公司统一安排下,重庆奥林特机电技术有限公司调配专业力量,对两台设备上管箱内的全部管子-管板角焊缝,进行了彻底的修复处理。
现将修复过程及相关技术心得,简要介绍如下。
1 设备概况
1.1 设备技术特性
高压甲铵冷凝器主要设备技术特性如表1、表2。
表1 EA101主要设备技术特性
介质
参数 |
壳 侧 |
管 侧 |
蒸汽 |
NH3 /CO2/甲铵液 |
设计压力MPa |
0.8 |
18 |
操作压力MPa |
0.49 |
17.1 |
设计温度℃ |
200 |
220 |
操作温度℃ |
158/158 |
183/176 |
材 质 |
SA516M Gr.485 |
DP-12 |
列管规格 |
¢19×2×10300 |
2820根 |
表2 EA102主要设备技术特性
介质
参数 |
壳 侧 |
管 侧 |
蒸汽 |
NH3 /CO2/甲铵液 |
设计压力MPa |
2.1 |
18 |
操作压力MPa |
1.72 |
17.1 |
设计温度℃ |
190 |
220 |
操作温度℃ |
137/155 |
183/176 |
材 质 |
SA240 316L-VG |
DP-12 |
列管规格 |
¢19×2×10300 |
1735根 |
换热管材料牌号为SA240/NAR DP-12,其化学成分见表3。
表3 DP-12化学成分
C |
Si |
Mn |
P |
0.03 |
0.75 |
1.1 |
0.03 |
S |
Cr |
Ni |
Mo |
0.03 |
24.8~26 |
6.5~7.5 |
2.5~3.2 |
Cu |
N |
W |
|
0.2~0.4 |
0.1~0.3 |
0.1~0.3 |
1.2 设备腐蚀形貌
2008年大修时检查发现:管子-管板角焊缝存在严重的复相晶间腐蚀,和2007年相比,腐蚀加剧趋势明显。
具体表征为:表层金属组织大面积疏松脱落、收弧点发黑溃烂、焊肉局部穿孔。
腐蚀形貌见图片1、图片2、图片3。
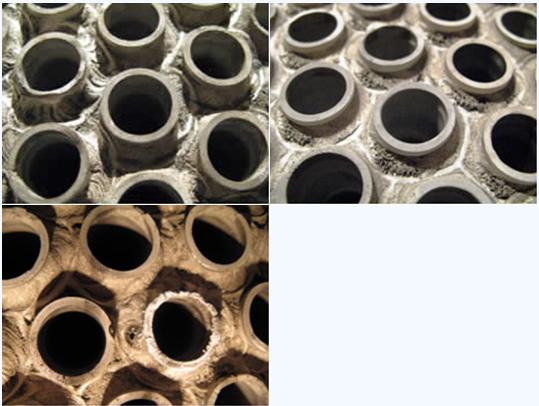
2 修复技术准备
2.1 修复思路的确定
1)修复范围:
针对设备实际腐蚀现状,参考国外相同设备的泄漏事故,本着预防性的原则,决定将两台设备上管箱内的全部管子-管板角焊缝进行修复。
2)原管子-管板角焊缝焊肉的清除:
由于腐蚀因素,原有制造形成的表层焊肉已经不再是稳定的奥氏体-铁素体双相组织;若直接在上面补焊,则一定时间后,表层金属一旦腐蚀,将直接面临新的泄漏危险。
因此,我们确定了先将旧焊缝表层焊肉彻底清除,再重新焊接的修复原则。
3)焊接方式:
由于现场修复与实际制造的工况差别,因此,不考虑使用管子-管板自动焊,而是采用传统的手工钨极氩弧焊。
4)焊接材料:
根据腐蚀试样的试验结果,采用25-22-2型纯奥氏体焊丝和DP-3型双相钢焊丝,均可满足耐蚀性能要求;其中,25-22-2材料与DP-12材料进行异种钢焊接获得的焊缝组织更加稳定,焊接质量容易控制。
但,在日本东洋工程公司的强烈坚持下,由于其有成熟的焊接工艺评定等原因,最终确定采用DP-3型双相钢焊丝。
其牌号为SUS329J4L DP-3T(UNS S39226),化学成分见表4。
表4 DP-3T化学成分
C |
Si |
Mn |
Ni |
Cr |
0.01 |
0.37 |
0.78 |
9.3 |
25.3 |
Mo |
Cu |
W |
N |
|
3.03 |
0.4 |
0.27 |
0.17 |
|
2.2 焊肉清除机具的选择
由于双相钢本身硬度较高,腐蚀后其表面产物相当硬脆,普通的打磨方式无法进行有效清除,必须采用机械切削。
经对比试验,我们最终选择了日立造船出产的气动式管端加工机。
其优点在于:利用换热管内壁定心,简便可靠;内置式气动马达,无级调速,可任意变换切削速度以控制切削力大小;合金刀片双面对称安装,可计数进刀量控制,能有效保证加工精度。
2.3焊接器具及背保护工装的准备
1)焊接器具:
为了从施工器具的角度保障焊接可靠,我们选择了ESAB LTN-250A焊机,气冷式焊炬内置周向滤网以保证气流稳定性,喷嘴直径¢10,钨极直径¢2。
2)背保护工装:
为避免列管内壁热影响区氧化,焊接时管内应通氩实现被保护。
我们专门设计制作了背保护工装,通氩气的嘴子内装有不锈钢丝网,可使通道截面积尽量增大,使氩气从保护嘴送出分布在所有焊接时有可能达到400℃以上的管壁区域,并由列管顶端逸出。
2.4焊接工艺评定及焊工考试
1)焊接工艺评定:
由东洋工程公司提供原始制造使用的焊接工艺评定供参考。
实际使用时,和原始工艺评定相比,主要存在以下不同:
①焊接层数不同。
本次修复焊接不存在原始制造时的打底层;
②焊接材料不同。
本次焊接使用的DP-3T焊丝,为原始制造时使用焊丝的改良型。
③焊接规范的修正:
在东洋工程公司提供焊接工艺评定的基础上,出于减小修复焊接过程对换热管原内壁热影响区热输入量的考虑,我们建议对焊接规范进行了以下修正,并得到了东洋工程公司的认可。
主要调整了焊丝直径,减小了焊接电流,控制管壁熔深及管内壁热影响区颜色更为严格,
2)焊工考试:
采用东洋工程公司提供的考试试件进行。
钢板(模拟管板耐蚀层)厚度为30mm,材料为DP-12型;换热管材料、规格与设备内实际相同;焊丝采用DP-3T ¢1.2/1.6,共焊接两层。
按与实际状况相同的列管间距、管端伸出高度进行试件的加工、组装。
焊接完毕后,由奥林特公司现场技术负责人会同日方技术代表共同进行以下项目的考核验收:
①宏观检查焊缝、管桥三角区外观成型及管端完整性;
②对焊缝及管桥三角区进行PT检测;
③将试件剖开,对断面进行宏观检查,重点是管壁熔深及换热管外壁与管板结合根部熔合状况;
④对断面进行金相检查。
共8名焊工,每人焊接1块试件计20根换热管。
考试结果为:7人一次合格,1人经再培训后合格。
2.5 修复过程主要质量控制点的建立
为确保修复质量,建立控制点如表5,并组成专门质量检查组,按规定时间表进行检查控制。
表5 修复质量控制点明细
检查项目 |
检查内容摘要 |
检查类别 |
机械加工 |
加工位置、加工尺寸 |
W |
第一层
焊接 |
焊接参数、焊接材料 |
W |
焊缝成形、焊肉表面气孔、焊缝收弧缩孔、管壁熔深、管板三角区凹陷及是否存在漏焊 |
H |
PT检测 |
H |
第二层
焊接 |
焊接开始前确认:
缺陷已经全部返修、全部PT检测合格、无漏焊 |
H |
焊接参数、焊接材料 |
W |
焊缝成形、焊缝腰高、焊肉表面气孔、焊缝收弧缩孔、管壁熔深、管板三角区凹陷及是否存在漏焊 |
H |
PT检测 |
H |
交付氨渗漏前确认:
缺陷已经全部返修、全部PT检测合格、无漏焊 |
H |
氨渗漏试验 |
壳侧氨渗漏 |
H |
压力试验 |
管程气压试验 |
H |
说明:W为现场确认,H为检查停止点。
3 修复过程重点环节及质量要求
3.1 机械加工
清除原焊缝表层焊肉,并形成新的焊接坡口。
1)几何尺寸:
按图1所示。
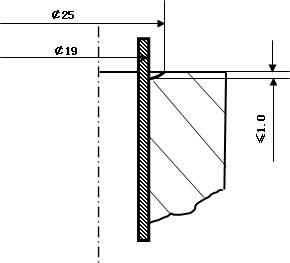
2)外观质量:
管外壁无加工损伤;加工面宽窄均匀,管桥三角区无明显凸起;加工面无明显腐蚀产物残留。
3.2第一层焊接
1)焊接参数:
焊接电流 |
外侧保护气 |
内侧保护气 |
焊丝直径 |
70-80A |
10~15L/min |
5~10L/min |
¢1.2 |
2)操作要求:
①瞄准钨极位置角度大约10°,绝对避免将钨极朝向管外侧。见图2所示。
②采用高频,在管板起弧,从焊接部位外侧送入焊丝,控制管壁熔深在0.3~0.8mm,最大不得超过1.0mm。
③管子外壁与管板的结合根部必须焊透,送丝量要保持足够以免焊缝凹陷;
④收弧采取延时冷却;最终收弧点处理方式为重熔或部分打磨,收弧部位要比其它焊接部位高出1.0mm左右。
⑤钨极尖磨损后要及时更换。
⑥为了防止温度上升,不要连续焊接相邻的管子;采取分道间断焊接,每根列管角焊缝分三次焊完,即逆时针方向每次焊120度角。
3)焊缝外观成形及尺寸:
按图4所示进行控制。
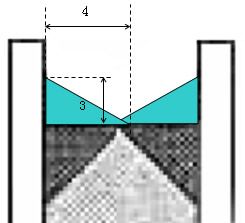
4)宏观检查:
①焊缝成形:按图4要求,不允许凹陷部位的存在。
②外观缺陷:不允许任何的焊肉表面气孔、焊缝收弧缩孔、咬边、裂纹、焊肉过大。
③内壁热影响区:颜色只能为正常的银色或金黄色,允许局部浅蓝色存在,不得存在深蓝色及内壁烧穿现象。
④换热管端:除由于管端已经存在的原腐蚀减薄及缺口而造成的塌焊以外,不得允许管端熔化现象的存在。
5)渗透探伤:
①焊接后冷却到40℃进行;
②不允许有任何线性及孔型缺陷的存在;凡发现前述类型缺陷,必须返修;
③探伤确认完后清理表面,用脱盐水冲洗+钢丝刷清理方式,除去表面残留的显像剂,以免影响下一层焊接质量。
6)焊缝返修:
①过程返修:焊接过程中,焊工自行发现的缺陷,可按返修技术作业程序自行进行。
②通知返修:宏观检查及渗透探伤发现的缺陷,在接到返修通知后进行。
③返修技术作业程序:焊接冷却到40℃后,用笔式砂轮打磨消除缺陷,再按焊接要求对返修部位进行补焊;补焊部位焊肉要比其它焊接部位高出1.0mm左右。
④返修后质量确认:除进行宏观检查确认外,还必须进行二次渗透探伤。
3.3第二层焊接
1)焊接参数:
焊接电流 |
外侧保护气 |
内侧保护气 |
焊丝直径 |
80-90A |
10~15L/min |
5~10L/min |
¢1.6 |
2)操作要求:
与第一层焊接相同。
3)焊缝外观成形及尺寸:
按图5所示进行控制。
4)管桥三角区成形:
管桥三角区不得形成凹坑,焊接时必须补平。见图6所示。
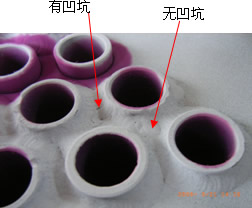
5)宏观检查:
除焊缝成形及官桥三角区外观按图5、图6所示要求进行检查外,其余检查要求与第一层焊接相同。
6)渗透探伤:
与第一层焊接相同。
7)焊缝返修:
与第一层焊接相同。
3.4最终检验确认:
由于现场不具备在氨渗漏试验之前进行水压试验的条件,故最终检验确认手段为氨渗漏试验+管程气压试验。
1)氨渗漏试验:
按HG/T 3176-2002《尿素高压设备氨渗漏试验方法》规定,进行壳侧氨渗漏试验。
2)管程气压试验:
结合系统开车升压过程进行,压力至操作规定值。
4 修复质量检验结果
4.1 第一层焊接
1)宏观检查后返修率3%,主要返修原因在于气孔的处理;
2)PT检测后返修率1%,主要返修原因仍然是气孔的处理。
4.2 第二层焊接
1)宏观检查后返修率0.5%,主要返修原因在于官桥三角区凹陷;
2)PT检测后无返修。
4.3 氨渗漏试验
一次合格。
4.4 管程气压试验
一次合格。
4.5 遗留问题
1)原内件支撑螺柱附近,共约0.5%的换热列管,管端被电弧熔塌形成小缺口,但缺口底部均高于焊缝,故不再处理。
2)管板边缘部位,共约0.3%的换热列管,靠管箱筒体侧,内壁热影响区颜色发蓝,保留观察。
5 运行一年后实际效果
2010年3月,我们对两台设备修复焊接部位,进行了全面的腐蚀检查。
检查结果发现:全部修复焊缝表面钝化良好,金属光泽明显,不存在异常腐蚀缺陷;原遗留的局部管内壁发蓝处,无疏松条带存在;原遗留的局部管端熔化形成缺口处,无腐蚀沟槽形成。
实际腐蚀形貌见图片4、图片5。
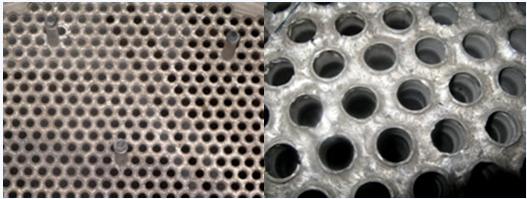
6 结束语
1)双相钢焊缝腐蚀产物的清理,采用机械切削方式最为有效快捷;
2)焊接方案的制订、焊工的技能培训、焊接工艺纪律的执行、焊接检验控制点的确立,是保障修复施工质量的基础;
3)在管子-管板角焊缝的修复焊接过程中,控制管壁熔深是关键,焊接气孔的处理是难点。
作者简介:余竹君,男,42岁,1988年毕业于重庆大学机械工程系,高级工程师,重庆奥林特机电技术有限公司副总经理。长期从事尿素高压设备腐蚀监测与维修的技术管理,先后参加过尿素高压设备的腐蚀行为研究、耐蚀材料国产化研制、修复技术开发及应用等多项国际国内合作课题。